The Ontario Government is Committing to 5,000 New Apprenticeships Each Year for the Next Four Years
tradesmart23
on
March 18, 2025
The Ontario Government is Committing to 5,000 New Apprenticeships Each Year for the Next Four Years

Introduction: A Step Forward, but Not the Full Solution
The Ontario government has announced funding to create 5,000 new apprenticeship spots annually for the next four years, a move that signals a commitment to strengthening the skilled trades workforce. Given the severe shortage of tradespeople, this investment in apprenticeship training is a necessary and positive step. However, it is crucial to understand who is eligible for these opportunities and whether this initiative will genuinely help solve Ontario’s trades shortage.
The reality is that getting an apprenticeship spot is not the hardest part of entering the trades—getting that first job is. These 5,000 new seats will help existing apprentices complete their required schooling, but they do nothing for those who have yet to be signed on as apprentices in the first place. That’s where programs like Trade Smart College’s pre-apprenticeship training, which blends professional and technical skills with a six-month paid internship, play a crucial role in actually helping people enter the trades.
Who is Eligible for These New Apprenticeships?
A common misconception is that apprenticeship schooling—sometimes called “trade school”—is where people go to learn a trade from the ground up. This is not the case. Apprenticeship schooling is only for people who are already apprentices. To qualify for one of these new apprenticeship seats, an individual must have already been hired by an employer and registered with the Ontario apprenticeship system.
To put it simply, you cannot walk into a college and sign up for an apprenticeship program. You must first have an employer sponsor you, sign an apprenticeship training agreement, and receive an official apprenticeship number before being eligible for Level 1 training. Only publicly funded colleges, unions, and select registered training providers can offer apprenticeship schooling, and career colleges, including Trade Smart College, are not eligible to offer this training.
How Will This Help Existing Apprentices?
For those who are already apprentices, these additional seats will be beneficial. Currently, Ontario has a backlog of apprentices who struggle to access the mandatory in-school portion of their training. The government funding will help ease this bottleneck, allowing more apprentices to move through Level 1, Level 2, and Level 3 training without delays.
This is a positive step for productivity, as more apprentices completing their education means more skilled tradespeople advancing toward journeyperson status. However, this investment is only addressing the needs of those who have already secured an apprenticeship—it does nothing to increase the number of people entering the trades. And that is where the real problem lies.
The Hardest Part of Entering the Trades: Getting That First Job
The true barrier to solving Ontario’s trades shortage isn’t a lack of apprenticeship seats—it’s the challenge of getting hired as an apprentice in the first place. The process of securing that first apprenticeship job is notoriously difficult. Employers are hesitant to take on inexperienced workers because, quite simply, they don’t want to train someone who isn’t prepared, focused, and reliable.
Right now, there are two main ways people get hired as apprentices. One is through personal connections. If you have a family member or friend in the trades, your chances of landing an apprenticeship improve significantly. However, relying on who you know is not a scalable solution for Ontario’s workforce needs. The second is through pre-apprenticeship programs. These programs exist to help people gain foundational skills and experience to make them more attractive to employers. However, most government-funded pre-apprenticeship programs simply replicate the Level 1 curriculum without addressing the professional skills gap that prevents many job seekers from getting hired.
What Skills Do Employers Look for in an Apprentice?
Employers are not just looking for technical knowledge. The single most important factor in hiring an apprentice is professionalism. A company cannot afford to invest time and resources into someone who lacks the ability to be punctual, adaptable, and productive.
The most in-demand skills that separate successful apprentices from those who struggle to find work include reliability, which means showing up on time and ready to work, and a strong work ethic, demonstrating a willingness to take initiative and do the job right the first time. Communication skills are also critical, as apprentices must be able to follow instructions, ask questions, and work as part of a team. Problem-solving ability is another key factor, as tradespeople need to think critically and adjust to real-world challenges. Adaptability is essential, as the industry is constantly evolving, and workers must be prepared to learn new techniques and technologies.
While technical skills can be learned on the job, professional skills must be developed before an employer will take a chance on a new apprentice.
Does This Government Funding Solve Ontario’s Trades Shortage?
The short answer is no. While adding 5,000 apprenticeship spots per year will help current apprentices complete their training, it does nothing to bring new people into the trades.
A true solution to Ontario’s skilled labour shortage must include a clear and accessible pathway for new workers to get their first job in the trades. This means increasing employer incentives to hire apprentices, expanding paid work experience opportunities, and improving pre-apprenticeship programs to emphasize professional and technical skills equally.
Key Takeaways
- The 5,000 new apprenticeship seats each year will only benefit those who are already registered as apprentices—not those looking to enter the trades.
- The hardest part of starting a career in the trades is getting that first apprenticeship job, not completing apprenticeship schooling.
- Many people struggle to find an apprenticeship because they lack professional skills, which employers prioritize over technical knowledge.
- The government’s plan does not address the real problem: the need for more entry-level pathways into the trades.
The Bottom Line: Getting Into the Trades Still Requires More Than Just Government Funding
While Ontario’s investment in apprenticeship schooling is a positive step, it does not solve the biggest problem facing the trades industry: getting more people hired as apprentices in the first place. Without a clear pathway for new workers to gain professional and technical skills before entering the trades, the labour shortage will persist.
At Trade Smart College, we bridge this gap by preparing students with both the professionalism and technical expertise that employers demand. Our six-month paid internship ensures that graduates enter the workforce prepared, focused, and reliable, increasing their chances of securing an apprenticeship. Real solutions to Ontario’s trades shortage start with getting people into the industry—not just funding the ones who are already there.
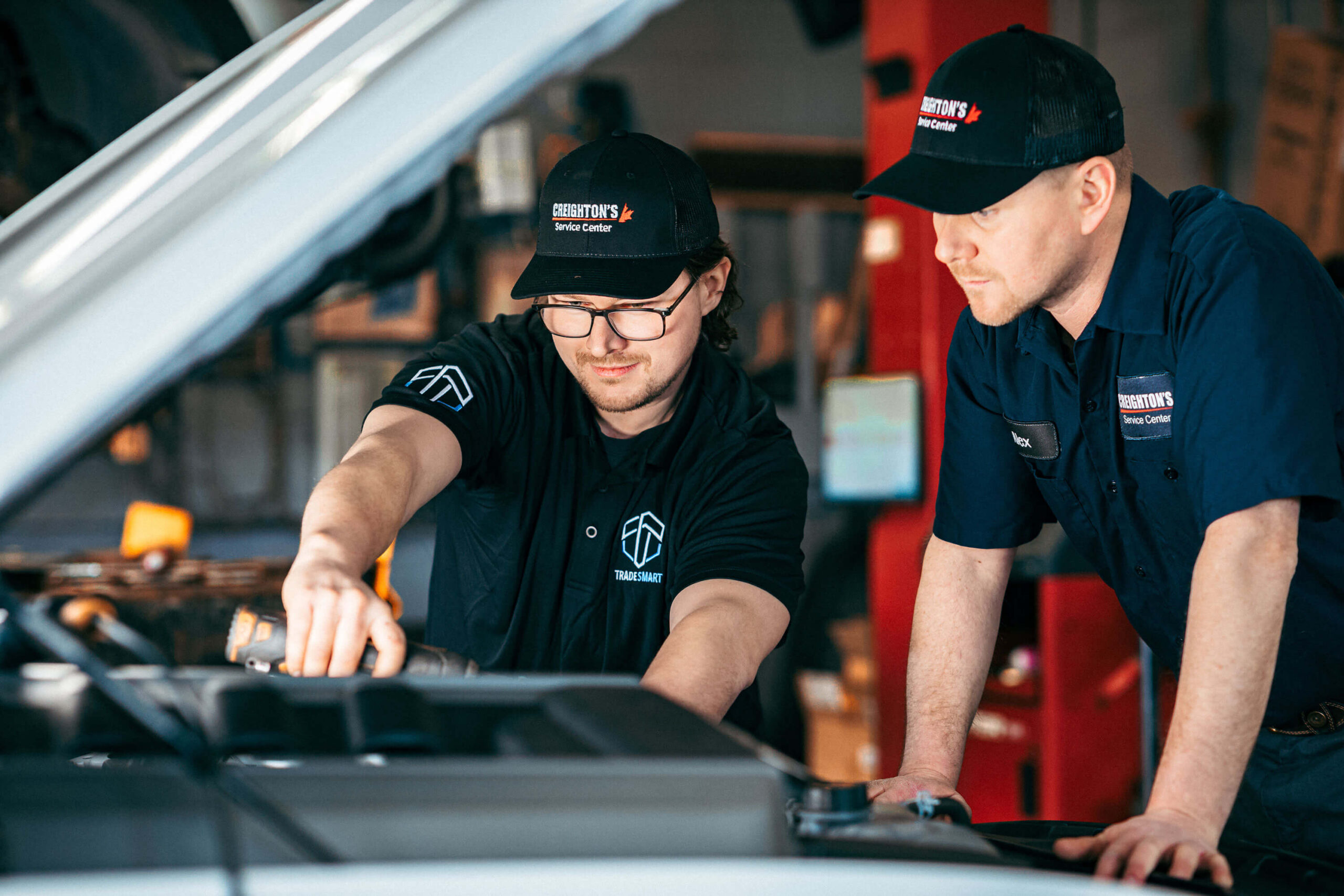
We Need More People in the Skilled Trades
We Need More People in the Skilled Trades For decades, we’ve been hearing about the shortage of people entering the skilled trades, and it seems like the problem is getting worse, not better.
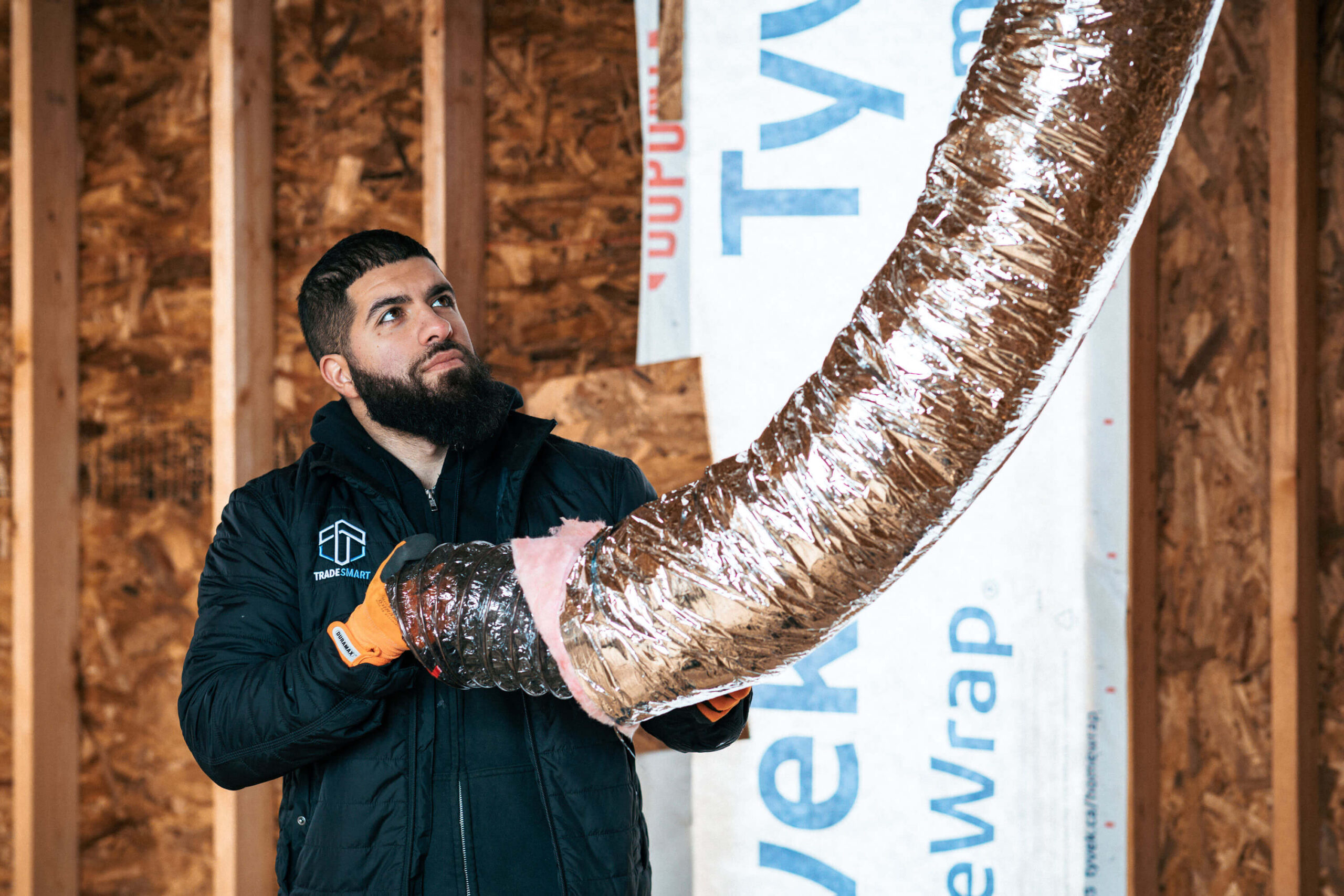
Your Chances of Getting an Apprenticeship in Ontario: By the Numbers
Your Chances of Getting an Apprenticeship: By the Numbers By any measure, Ontario is desperately short of skilled tradespeople. We need people now, but the first step in becoming a tradesperson is to
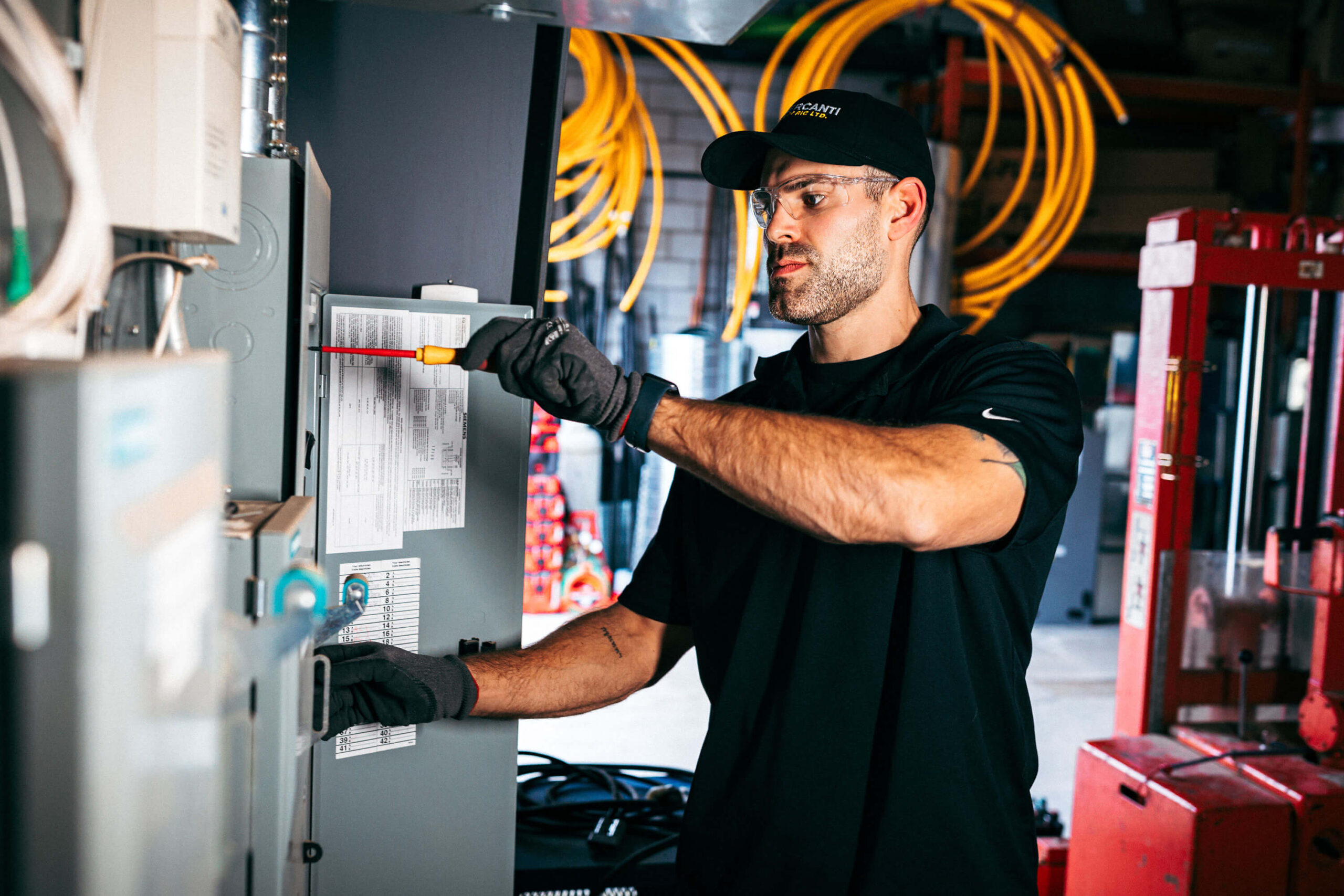
What’s the Highest Paying Trade in Ontario in 2024?
What’s the Highest Paying Trade in Ontario in 2024? Many of our prospective students ask some version of the question, “what is the highest paying trade in Ontario?” We understand the impulse behind
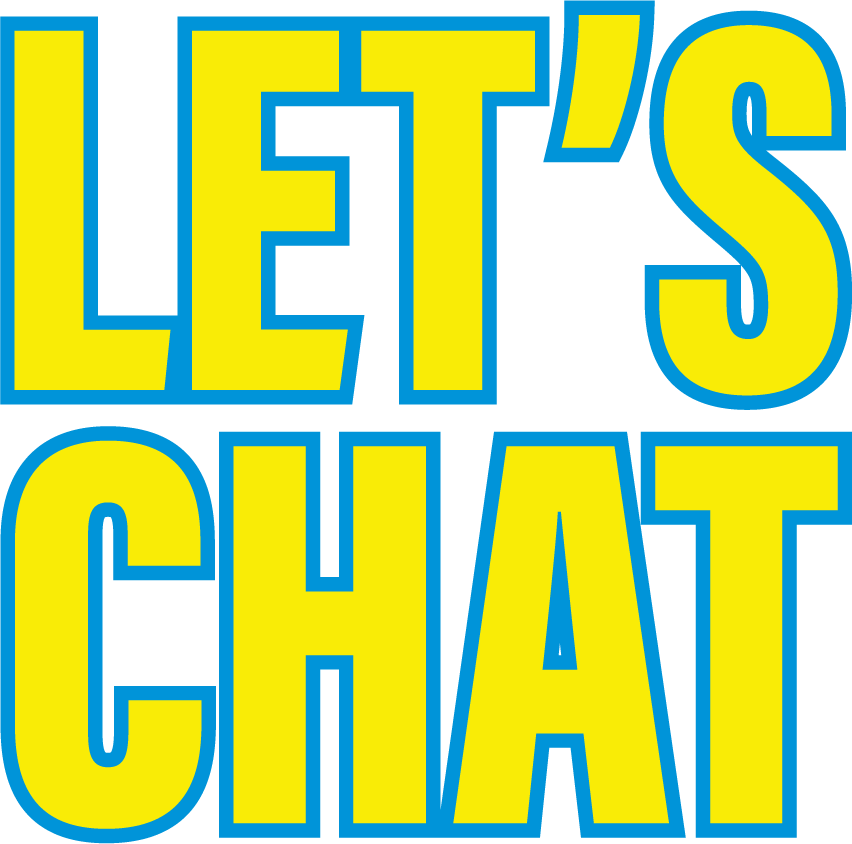
Your Meeting
Your Terms
Need more info? Looking to register? Want to find out about financing or start dates? Book a call, meeting, or text chat with Carrie our Student Success Manager.
Contact the Team
Campus Hours
- Mon- Fri: 7am- 5pm
- Open House - See Schedule